13 Mar De top vijf productiviteitsmoordenaars in de PCB-industrie
Sommige oplossingen
De weg naar het maximaliseren van de productiviteit op de fabrieksvloer ligt in een top-downbenadering die de gedetailleerde operationele punten in de vorige paragrafen behandelt. Er moeten stappen worden ondernomen op de volgende gebieden: Gegevensvoorbereiding Productieprocessimulatie Productieprocesvoorbereiding Productieuitvoeringssystemen Voor al deze uitdagingen zijn technische oplossingen nodig. En, cruciaal, er moeten rapportagesystemen zijn voor ingenieurs, lijnoperators en productiemanagers die de specifieke acties identificeren die moeten worden genomen om de prestaties te verbeteren. Bovendien moet de informatie tijdig genoeg zijn om verbeteringen aan te brengen voordat de kans verloren gaat en zich elders nieuwe problemen voordoen. Gegevensvoorbereiding Aandacht voor gegevensvoorbereiding voor zowel de invoer van het componentmodel als de invoer van ontwerpgegevens is een verplichte eerste stap: Componentmodellering – Fabrikanten moeten nauwkeurige fysieke modellering invoeren van alle onderdelen die ze op de lijn willen gebruiken, inclusief pincontacten voor soldeer verbindingen, geïntegreerd met de CAD-gegevens. Dit moet het volgende omvatten: Consistente, CAD-bibliotheekneutrale modellering van de onderdelen om gestandaardiseerde DFM- en procesvoorbereidingsfuncties stroomafwaarts mogelijk te maken. Genormaliseerde offset van componenten, rotaties en polariteitsverklaringen naar een standaard. De wereldwijde elektronica-industrie heeft een omzet van $ 750 miljard, waarvan tweederde voor rekening van PCB-assemblage. PCB-productie wordt gekenmerkt door een obsessieve drang naar hogere productiviteit in de context van drie belangrijke industriële drijfveren: Kortere productlevenscycli – De druk staat op het ontwikkelen van betere producten en deze op de markt te brengen voordat de concurrentie dat doet, tegen lagere kosten, terwijl tegelijkertijd de product van de volgende generatie. Nog maar vijf jaar geleden werden productlevenscycli gemeten in jaren; nu worden ze gemeten in maanden, wat druk uitoefent op ontwerpers en fabrikanten om het proces van de prototypefase naar de productie van grote volumes te versnellen. Meer complexiteit - Fabrikanten produceren complexere ontwerpen met een hogere dichtheid met meer miniaturisatie en meer geavanceerde borden. Een typische stuklijst (BOM) voor een PCB-assemblage kan nu in totaal duizenden onderdelen bevatten, samengesteld uit honderden unieke regelitems. De "ingekochte" items - condensatoren, weerstanden, diodes enzovoort - hebben elk een of meer "alternatieve onderdelen" om minimale stuklijstkosten en maximale beschikbaarheid van onderdelen mogelijk te maken. Complexere stuklijsten (BOM) leggen een premie op een hogere componentkwaliteit en betere traceerbaarheid. Outsourcing groeit snel - Kortere productlevenscycli en toegenomen complexiteit hebben OEM's gedwongen om outsourcing te omarmen, nu het snelst groeiende segment van de PCB-industrie. Electronics Manufacturing Service (EMS)-bedrijven waren in 21 goed voor 2004% van de markt, maar hun aandeel zal tegen 30 ongeveer 2008% bedragen. De totale markt zal in die tijd slechts 16% groeien. EMS-providers bieden lagere prijzen, snellere marktintroductie en betere orderafhandelingsprestaties, omdat ze gebruikmaken van enorme geaggregeerde koopkracht die is afgeleid van het bedienen van honderden verschillende klanten, en door hun productiemiddelen te consolideren en te beheren om minimale eenheidskosten te bereiken. EMS-aanbieders richten zich op hun kerncompetentie van fabricage en inkoop van componenten; OEM's zijn vrij om zich te concentreren op het ontwerp en de marketing van nieuwe producten. Deze trends in de sector worden goed begrepen en hebben ertoe bijgedragen dat PCB-assemblage een van de meest concurrerende industrieën ter wereld is geworden. Onder druk om kosten te besparen en tegelijkertijd de opbrengsten en de marktintroductietijd te verbeteren, wordt gezocht naar die veranderingen in de fabrieksactiviteiten die het concurrentievermogen kunnen verbeteren. Doorgaans wordt 60-70% van het geïnvesteerde kapitaal in vaste activa in de assemblage van printplaten opgesloten in de machines in de assemblagelijnen. SMT-assemblage is bijvoorbeeld bijzonder kapitaalintensief, met enkele lijnen die meer dan $ 1 miljoen kosten en de prijs stijgt. Managers van fabrieken die zwaar onder druk staan, vragen zich af hoe ze ervoor kunnen zorgen dat hun geïnvesteerde kapitaal maximale productiviteit en concurrentievermogen oplevert. Het antwoord ligt niet alleen op het niveau van de individuele machines, maar ook op het niveau van de complete lijn of fabrieksvloer. PCB-assembleurs gebruiken veel metingen van productieprestaties, van de productbijproductspecificaties van cyclustijd, lijnslagsnelheid en first-pass-opbrengst tot benchmarks op een hoger niveau zoals "BOM-conversiekosten" en rendement op aangewend kapitaal. Welke Key Performance Indicators (KPI's) ook worden gebruikt, het doel is om de maximale output van een acceptabel kwaliteitsproduct te genereren uit de beschikbare assemblagelijnen, materialen, armaturen en beschikbare personele middelen.
- Onderdelen chaos
- Inefficiënte lijnopstelling
- Langzamer dan optimale slagsnelheden
- Lage machinepiekprestaties
- PCB/proces-combinatie is suboptimaal
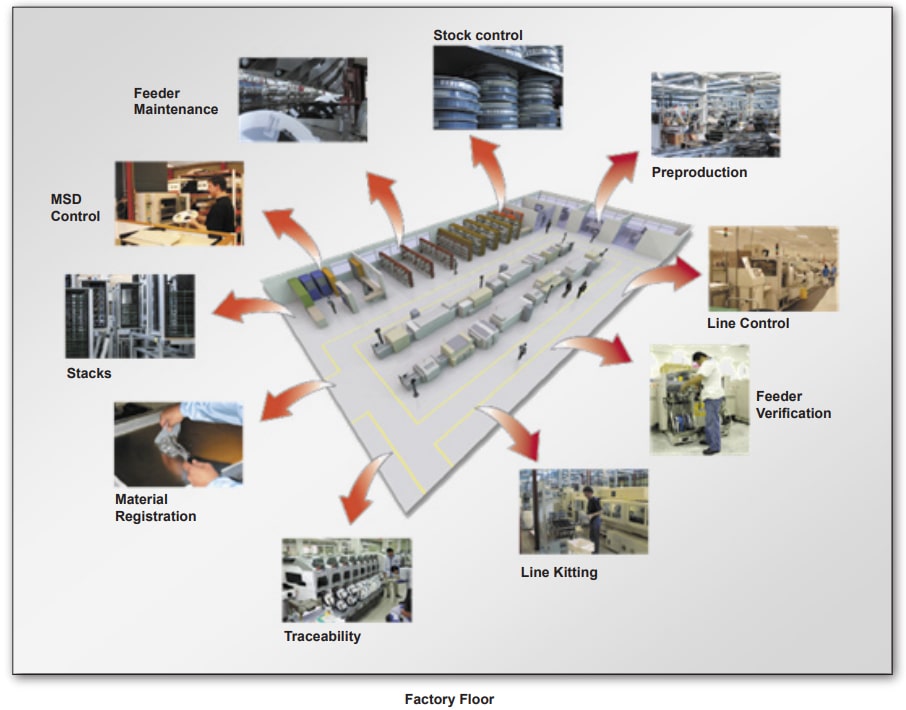
- Onderdelenchaos Het eerste probleem dat de productiviteit beïnvloedt, is dat materialen niet op het juiste moment op de juiste plaats zijn, klaar voor gebruik op de assemblagelijnen. Velen zijn van mening dat een volledige dekking in het ERP- of hoofdvoorraadbeheersysteem van alle te assembleren stuklijsten voldoende is. Maar de kritische factor is om de juiste hoeveelheden onderdelen en materialen beschikbaar te hebben en op het juiste moment op de machines te installeren wanneer dat nodig is. De massale verificatie van de beschikbaarheid van onderdeelnummers van componenten voorkomt niet dat de fabricage niet beschikbaar is vanwege het niet beschikbaar zijn van onderdelen op de fabrieksvloer, omdat:
i. Onderdelen die al zijn toegewezen aan andere opstellingen - Componenten voor montage op PCB's worden meestal in bulk verwerkt - ofwel op haspels met duizenden onderdelen of in stapels trays met honderden. Als dezelfde onderdelen tegelijkertijd nodig zijn voor twee productieorders, kan geen van beide lijnen correct worden ingesteld. Door de impact van dit probleem te vermenigvuldigen met de honderden componentspoelen of trays die aanwezig zijn op een typische PCB-fabrieksvloer, vergroot het risico dat niet in staat is om de juiste hoeveelheden onderdelen aan de lijnen te leveren voor elke productieorder, ondanks het feit dat, in totaal , komen de benodigde totale hoeveelheden onderdelen voor de productieorders overeen met de totale hoeveelheden onderdelen in het hoofdvoorraadbeheersysteem.
ii. Beschikbare onderdelen kunnen niet worden gevonden – In grote fabrieken volgen de ERP-systemen vaak materialen niet erg nauwkeurig zodra ze op de productievloer zijn vrijgegeven. Kerngegevens - over de lijn waaraan de onderdelen zijn toegewezen, of de opstellingen waarvoor ze zich inzetten nog in productie zijn en de exacte hoeveelheid onderdelen die in die opstellingen zijn vastgemaakt - ontbreken vaak. Hoewel uit de beschikbare gegevens blijkt dat de onderdelen beschikbaar zijn om met de productie te beginnen, kunnen ze vaak niet worden gevonden. Er ontstaan onnodige vertragingen aan het begin van een productierun terwijl "expediteurs" verwoed op zoek zijn naar ontbrekend materiaal. Evenzo, en vanwege hetzelfde gebrek aan zichtbaarheid van welke onderdelen waar zijn, kunnen onderdelen vaak onnodig aan een lijn worden geleverd, ter ondersteuning van de opbouw, terwijl er eigenlijk al voldoende voorraad van die onderdelen op de lijn is geladen, overgebleven van een vorige productieorder. Deze onnauwkeurigheden bij het volgen leiden tot onnodige verhogingen van de voorraadkosten op de fabrieksvloer. als gevolg van mis-picks of een defect aan de spuitmond vóór plaatsing. Over het algemeen dwingt dit PCB-fabrikanten tot overschatting
iii. Onderdelen in quarantaine – Een andere factor die de beschikbaarheid van onderdelen bij de pick-and-place-machine beïnvloedt, is de gevoeligheid van sommige categorieën componenten voor blootstelling aan normale atmosferische omstandigheden op de fabrieksvloer. Soms worden componenten na het uitpakken uit verzegelde containers aangetast door luchtvochtigheid en moeten ze al na een paar uur in een oven worden gebakken om het vocht van de componenten te verwijderen. Discontinuïteiten veroorzaakt door bakcycli in de oven betekenen dat bepaalde onderdelen cycli doorlopen van "beschikbaar" en "niet-beschikbaar" voor montage, ook al zijn ze altijd "op voorraad".
iv. Onnauwkeurig voorraadbeheer – De beschikbaarheid van onderdelen in het ERP-systeem is vaak onnauwkeurig als gevolg van niet-geregistreerde verspilling. Wanneer componenten na gebruik op de fabrieksvloer naar het magazijn worden teruggestuurd, is het lastig om een nauwkeurig beeld te krijgen van hoeveel onderdelen er nog op de haspel zitten. Moeten productiemanagers gewoon de starthoeveelheid nemen en het aantal plaatsingen dat op de stuklijst is gedefinieerd aftrekken? Waarschijnlijk niet, omdat het de onderdelen negeert die verloren gaan door de machinevoorraad, wat leidt tot onverwachte stock-outs op de fabrieksvloer bij volgende productieorders. Dure (en ongeplande) productieonderbrekingen zoals deze creëren de noodzaak om de materialen van de lijnen te verwijderen voor volgende bestellingen en dringende aankoop van onderdelen om tekorten te corrigeren. Onnauwkeurig voorraadbeheer dwingt ook tot de tijdrovende en kostbare praktijk van voorraadcontroles op de hele locatie, waarbij de productie in wezen wordt opgeschort terwijl de gegevens in het ERP-systeem handmatig worden gesynchroniseerd met de realiteit van de productievloer.
v. voorraadniveaus, wat leidt tot onverwachte stock-outs op de fabrieksvloer bij volgende productieorders. Dure (en ongeplande) productieonderbrekingen zoals deze creëren de noodzaak om de materialen van de lijnen te verwijderen voor volgende bestellingen en dringende aankoop van onderdelen om tekorten te corrigeren. Onnauwkeurig voorraadbeheer dwingt ook tot de tijdrovende en kostbare praktijk van voorraadcontroles op de hele locatie, waarbij de productie in wezen wordt opgeschort terwijl de gegevens in het ERP-systeem handmatig worden gesynchroniseerd met de realiteit van de productievloer.
- Inefficiënte lijnopstelling Een efficiënte SMT-assemblagelijn hangt af van het vermogen om honderden opstellingsvariabelen tegelijk te coördineren. Als een aspect van de lijnopstelling onjuist is, is de uitvoer van slechte kwaliteit het resultaat. Er zijn verschillende veelvoorkomende redenen voor het opzetten en debuggen van een trage lijn:
i. Instelinstructies komen niet overeen met machineprogramma's – In veel gevallen zijn de engineeringgegevens die op de lijnen binnenkomen afkomstig van meerdere, losgekoppelde gegevensstromen. De kitlijst voor elke machine wordt aangestuurd vanuit de stuklijst in het ERP-systeem, maar houdt geen rekening met de beslissingen over het splitsen en balanceren van stuklijsten die door de machineprogrammeurs worden genomen. CAM-systemen die worden gebruikt voor het genereren van machineprogramma's werken vaak vanuit een andere database dan het CAM-systeem dat wordt gebruikt om de fabrieksvloerreiziger te genereren. En CAM-systemen die worden gebruikt om AOI-machines te programmeren, zijn anders dan systemen die worden gebruikt om de pick-and-place-machines te programmeren. De versnippering van datastromen kan groot zijn; elk punt van ontkoppeling tussen technische databases biedt een andere mogelijkheid om niet-gesynchroniseerde gegevens of instructies voor verschillende delen van de assemblagelijnen te genereren. Alle installatiefouten moeten ofwel bij de bron worden geëlimineerd, door het ontwerp, of worden ontdekt in de "first-off" -fase en worden geëlimineerd door installatie-instructies te bewerken terwijl de lijn niet werkt en onproductief is
ii. Onderdelengegevens op de machines ontbreken of zijn onjuist - Elke SMT-pick-and-place-machine, AOI-machine en in-circuit tester heeft een bibliotheek met gegevens nodig om de belangrijkste kenmerken van elk te assembleren, inspecteren of testen onderdeel te beschrijven. Pas wanneer de componentenbibliotheek van de machine is gevuld met gegevens die de componenten voor de productieorder beschrijven, kan de machine zijn werk doen. Elk nieuw onderdeel dat op de fabrieksvloer wordt geladen, betekent dat de bibliotheekgegevens voor dat onderdeel in de machines moeten worden ingevoerd en geverifieerd. Als de gegevens eenmaal zijn aangemaakt, moeten ze ook goed worden beheerd, aangezien eventuele wijzigingen kunnen leiden tot onnodige uitvaltijd als ze niet worden uitgevoerd door een gekwalificeerde operator. Zonder een gecontroleerde en gecentraliseerde oplossing om de componentgegevens op machineniveau te beheren, moeten de gegevens nauwgezet worden ingevoerd in meerdere machines, wat onnodige uitvaltijd en een hoog risico op gegevensconsistenties tussen meerdere machines veroorzaakt.
iii. Volledige offline installatie wordt niet bereikt - Veel fabrikanten zijn niet in staat om offline componenten te laden en verificatie in te stellen. Dit dwingt de lijn af te breken en in te stellen voordat de productie kan beginnen, wat leidt tot verspillende uitvaltijd. Ongetwijfeld kunnen de totale voorraadkosten van de feeder worden geminimaliseerd door de installatie online uit te voeren, maar er wordt een hoge prijs betaald in termen van verloren lijnoutput en machinegebruik.
iv. Opstelling is onjuist in de eerste fase – Als de algehele lijnopstelling niet in het begin parallel met de voorraadcontrole wordt geverifieerd, moeten fouten worden gedetecteerd op het moment dat de eerste keer wordt geproduceerd. Dit is de duurste manier om een instellingsfout te vinden en te elimineren, aangezien de verstreken tijd tussen het maken van de fout en het detecteren wordt gemaximaliseerd. Vermenigvuldig de mogelijkheden voor fouten/detectie/reparatie op basis van het aantal feeders, machines, programma's en de mogelijkheid voor escalerende installatie-debug-tijd wordt duidelijk, in vergelijking met het verifiëren van elk aspect van de installatie terwijl deze wordt uitgevoerd. Zodra de eerste fase is voltooid en de lijn in volle productie is, is het ook van vitaal belang dat fouten worden vermeden wanneer nieuwe onderdelen op een machine worden geplaatst om een uitgeputte feeder aan te vullen. In het ergste geval worden verkeerd geplaatste onderdelen gedetecteerd na assemblage van de volledige batch, in de inspectie- of testfase. Dergelijke reparaties hebben maximale kosten en impact op de algehele productiviteit van de fabriek.
v. Het niet benutten van bestaande machineconfiguraties – De beste manier om stilstandtijd bij de installatie tot een minimum te beperken, is door de noodzaak te elimineren om lijnen te strippen en opnieuw in te stellen tussen productieorders. Vanwege de complexiteit van het beheer van de enorme verscheidenheid aan componenten, feeders, feederposities, componenthoeveelheden en de factoren die van invloed zijn op een geoptimaliseerde set-up voor minimale cyclustijd, verwijderen de meeste fabrikanten alle feeders en componenten van de lijnen tussen productieorders. Hierdoor blijft de controle behouden, maar wordt de productiviteit drastisch verminderd. Door productieorders vooraf te analyseren en productgroepen te identificeren die dezelfde opstelling (of het grootste deel van de opstelling) op een assemblagelijn kunnen delen zonder in onaanvaardbare mate in te leveren op de slagsnelheid, kunnen enorme besparingen in uitvaltijd worden bereikt. Het gebruik van productgroeperingstechnieken levert aanzienlijke productiviteitsverbeteringen op in bewerkingen met een hoog mix/laag tot gemiddeld volume, waarbij omschakelingen een van de belangrijkste bijdragen aan de uitvaltijd van de lijn zijn.
zag. Niet anticiperen op de vereisten voor het aanvullen van onderdelen – In productieomgevingen met een hoog volume en een lage mix is er onvoldoende vooruitgang voor een nauwkeurige, op simulatie gebaseerde benadering voor het programmeren van de lijn als geheel. ii. Machineprogrammering is niet gebaseerd op volledige kinematische simulatie – Als de simulatie en programmering (balancering) op lijnniveau worden gescheiden van de machineprogrammering, ontstaat er een conflict tussen beide; de balancering is afhankelijk van nauwkeurige informatie over individuele cyclustijden, en de machineprogrammering kan een andere machinecyclustijd genereren dan die wordt aangenomen door de lijnbalanceringsfunctie. De sleutel is een zeer nauwkeurige simulatie van de configuratie van elke machine (feeders, nozzles, ...) en zijn bewegingskinematica. Zonder nauwkeurigheid in de simulatie van de machinecyclustijd, zullen niet alleen de individuele machineprestaties eronder lijden, maar zal ook de lijn als geheel niet in balans zijn voor een optimale algehele output. zichtbaarheid van de noodzaak om onderdelen op de lijn bij te vullen is de belangrijkste oorzaak van uitvaltijd. Het ergste geval doet zich voor wanneer alle componenten in een feeder uitgeput zijn, maar het komt als een verrassing voor de lijnoperator (die honderden feeders tegelijk moet begeleiden). Dit dwingt de lijn naar beneden terwijl de feeder wordt verwijderd, een nieuwe haspel wordt geladen (ervan uitgaande dat deze bij de hand is) en de feeder opnieuw op de machine wordt geladen.
- Langzamer dan optimale slagsnelheden Zodra de lijnen zijn opgezet, komt de productie in zijn herhaalbare ritme, waarbij geassembleerde PCB's van de lijn komen met een vaste frequentie die wordt bepaald door de lijnbalans, machinemogelijkheden en het optimalisatieniveau dat in het product is ingebed. specifieke machineprogramma's zelf. Op dit punt wordt de productiviteit op een dure maar onzichtbare manier beïnvloed als lijnen niet zijn geprogrammeerd om met de maximaal mogelijke slagsnelheid te werken. Dit kan verschillende redenen hebben: i. Simulatie, BOM splitsen/balanceren en machineprogrammering worden niet uitgevoerd op het volledige lijnniveau - Individuele machines kunnen op een optimaal niveau worden geprogrammeerd, maar als een volledige lijnbenadering van de programmeertaak niet wordt gevolgd, op basis van een volledige kinematische simulatie van alle machines die deel uitmaken van de lijn, lijden de algehele prestaties, voornamelijk veroorzaakt door onevenwichtigheden in de werkbelasting van de machine. De cyclustijd, of slagsnelheid, van de lijn wordt bepaald door de langzaamste machine in de lijn, wat de noodzaak benadrukt van een nauwkeurige, op simulatie gebaseerde benadering voor het programmeren van de lijn als geheel.
ii. Machineprogrammering is niet gebaseerd op volledige kinematische simulatie – Als de simulatie en programmering (balancering) op lijnniveau worden gescheiden van de machineprogrammering, ontstaat er een conflict tussen beide; de balancering is afhankelijk van nauwkeurige informatie over individuele cyclustijden, en de machineprogrammering kan een andere machinecyclustijd genereren dan die wordt aangenomen door de lijnbalanceringsfunctie. De sleutel is een zeer nauwkeurige simulatie van de configuratie van elke machine (feeders, nozzles, ...) en zijn bewegingskinematica. Zonder nauwkeurigheid in de simulatie van de machinecyclustijd, zullen niet alleen de individuele machineprestaties eronder lijden, maar zal ook de lijn als geheel niet in balans zijn voor een optimale algehele output.
iii. Onderdelengegevens op machineniveau zijn niet geprogrammeerd voor optimale handlingprestaties - De onderdeelgegevens die door elke machine worden gebruikt, bepalen hoe de componenten moeten worden behandeld: met welke snelheid, met welk mondstuk, hoe lang moeten de verschillende verblijftijden zijn, welke offsets moeten gelden voor het ophaalpunt enzovoort. Het voltooien van de eerste stap is voldoende om te controleren of het product correct is geassembleerd, maar dit brengt geen effecten op de lage assemblagesnelheid aan het licht vanwege suboptimale verwerkingsinstructies die zijn ingebed in de onderdelengegevensbibliotheek van de machine. Een operator zal er soms voor kiezen om de plaatsingssnelheid van een onderdeel te verlagen om de montage te garanderen, waarbij vaak onderhoudsproblemen worden gemaskeerd die moeten worden aangepakt, terwijl de algehele productiviteit van de lijn aanzienlijk wordt verminderd. Net als bij de optimalisatie van de machineprogramma's zelf, is het zonder toegang tot gedetailleerde prestatiegegevens voor mensen vrijwel onmogelijk om deze effecten te identificeren; en zonder detectie kunnen ze niet worden gecorrigeerd.
- Lage machinepiekprestaties Met investeringen in lijnen die oplopen tot miljoenen dollars, is het duidelijk dat machines moeten worden onderhouden om zo lang mogelijk met maximale productiviteit te presteren. Er zijn echter veel aspecten van de machineconditie die een verraderlijk effect hebben op het verminderen van de algehele prestaties.
- Vacuümdruk mondstuk – Als dit buiten de specificaties valt, kunnen componenten vallen tijdens het transport tussen het ophaalpunt en hun positie op de printplaat.
- Kleverig wisselen van mondstukvacuüm – Als de vacuümschakelaar plakkerig is, leidt dit tot overslaan van de mondstukken. Om de componenten foutloos uit de feeder te halen, is een positieve en snelle omschakeling van de vacuümtoevoer naar de nozzles vereist. Hetzelfde geldt voor de plaatsing; langzaam of onnauwkeurig schakelen van het vacuüm veroorzaakt onnauwkeurige opname of plaatsing.
- Versleten feeders - Dit leidt tot hoge miss-pick-percentages. Componentfeeders zijn mechanische indexeerinrichtingen die na verloop van tijd slijten. Aangezien het mechanisme slijt bij normaal gebruik, neemt de nauwkeurigheid van de presentatie van het onderdeel voor ophaling af, wat leidt tot het niet correct picken, wat componenten en cyclustijd verspilt. iv. Slechte onderhoudsinstructies - SMT-lijnen plaatsen componenten met snelheden van tien- of honderdduizenden onderdelen per uur. Deze razendsnelle machinesnelheid maakt het moeilijk om afnemende prestaties waar te nemen. Miss-picks gebeuren te snel om gezien te worden, maar een vertraging van een paar milliseconden op een herhalende functie leidt tot ontstemde prestaties. Zonder nauwkeurige en tijdige melding van waar de prestatieverminderingen zijn, hebben lijnoperators en onderhoudspersoneel weinig kans om de juiste actie te ondernemen om de prestaties te verbeteren.
- Slechte onderhoudsinstructies - SMT-lijnen plaatsen componenten met snelheden van tien- of honderdduizenden onderdelen per uur. Deze razendsnelle machinesnelheid maakt het moeilijk om afnemende prestaties waar te nemen. Miss-picks gebeuren te snel om gezien te worden, maar een vertraging van een paar milliseconden op een herhalende functie leidt tot ontstemde prestaties. Zonder nauwkeurige en tijdige melding van waar de prestatieverminderingen zijn, hebben lijnoperators en onderhoudspersoneel weinig kans om de juiste actie te ondernemen om de prestaties te verbeteren.
- bliksem machine snelheid maakt het moeilijk om afnemende prestaties te observeren. Miss-picks gebeuren te snel om gezien te worden, maar een vertraging van een paar milliseconden op een herhalende functie leidt tot ontstemde prestaties. Zonder nauwkeurige en tijdige melding van waar de prestatieverminderingen zijn, hebben lijnoperators en onderhoudspersoneel weinig kans om de juiste actie te ondernemen om de prestaties te verbeteren.
- PCB/proces-combinatie is suboptimaal PCB's kunnen worden ontworpen om assemblageprocesvriendelijk of procesvijandig te zijn. De meeste PCB's kunnen uiteindelijk worden geassembleerd, maar hogere kosten dan nodig vanwege een suboptimaal ontwerp, herbewerkingsniveaus en lijnefficiëntie variëren als gevolg van ontwerpkenmerken zoals:
i. De printplaat is niet machine- of lijnvriendelijk - de ijkpunten zijn verborgen, componenten conflicteren met transportbanden, het ontwerp van het montagepaneel is niet optimalisatievriendelijk. Ontwerpbeperkingen, zoals de distributie van componenten op het bord of variatie op de stuklijst, zijn zodanig dat één type machine geen lage plaatsingskosten kan bereiken en dit wordt pas zichtbaar als het product op de lijn wordt uitgevoerd.
ii. Soldeersjabloonontwerp leidt tot suboptimale soldeerverbindingen - Dit resulteert in veel nabewerking. Het primaire doel van assemblage is het creëren van betrouwbare soldeerverbindingen. Afgezien van een goede controle over het soldeerproces, moet de combinatie van componentpen, kussenpatroon en soldeersjabloon-opening worden geoptimaliseerd om het proces de beste kans te geven om verbindingen te bereiken die binnen acceptabele toleranties vallen (meestal gemeten in tientallen slechte verbindingen, per geproduceerd miljoen).
iii. De lay-out van het PCB-ontwerp stimuleert buigen en draaien - De panelen van PCB's die op de lijn worden geladen voor montage, moeten perfect vlak zijn, om "ophangen" van de transportband en verwerkingsfouten in de machines te voorkomen. Door de PCB te ontwerpen met een gelijkmatige verdeling van koper in alle assen, wordt de neiging van de PCB om te buigen en te draaien tijdens de verwerking geminimaliseerd.
iv. Pad/track-patronen moedigen tombstones aan tijdens reflow - Met de trend naar kleinere passieve chipcomponenten, zoals de 0201-pakketten die nu in volume worden verwerkt, is het ontwerp van pad- en trackpatronen om gelijke warmteafvoerende effecten aan weerszijden van de component mogelijk te maken van toenemend belang. Naarmate de componenten lichter worden, wordt het effect van oppervlaktespanningseffecten tijdens reflow belangrijker; als de ene kant terugvloeit voor de andere, kan oppervlaktespanning ervoor zorgen dat de droge kant van het gewricht omhoog komt, waardoor het "grafsteen" -effect ontstaat.
Sommige oplossingen
De weg naar het maximaliseren van de productiviteit op de fabrieksvloer ligt in een top-downbenadering die de gedetailleerde operationele punten in de vorige paragrafen behandelt. Er moeten stappen worden ondernomen op de volgende gebieden: Gegevensvoorbereiding Productieprocessimulatie Productieprocesvoorbereiding Productieuitvoeringssystemen Voor al deze uitdagingen zijn technische oplossingen nodig. En, cruciaal, er moeten rapportagesystemen zijn voor ingenieurs, lijnoperators en productiemanagers die de specifieke acties identificeren die moeten worden genomen om de prestaties te verbeteren. Bovendien moet de informatie tijdig genoeg zijn om verbeteringen aan te brengen voordat de kans verloren gaat en zich elders nieuwe problemen voordoen. Gegevensvoorbereiding Aandacht voor gegevensvoorbereiding voor zowel de invoer van het componentmodel als de invoer van ontwerpgegevens is een verplichte eerste stap: Componentmodellering – Fabrikanten moeten nauwkeurige fysieke modellering invoeren van alle onderdelen die ze op de lijn willen gebruiken, inclusief pincontacten voor soldeer verbindingen, geïntegreerd met de CAD-gegevens. Dit moet het volgende omvatten: Consistente, CAD-bibliotheekneutrale modellering van de onderdelen om gestandaardiseerde DFM- en procesvoorbereidingsfuncties stroomafwaarts mogelijk te maken. Genormaliseerde componentoffset, rotaties en polariteitsverklaringen naar een standaard.
Geen reacties